The Evolution of Automation in the Mining Industry
Automation in the mining industry has come a long way from its humble beginnings. The early stages of automation involved basic technologies like remote-controlled equipment and teleoperation systems. These innovations paved the way for more sophisticated automation solutions that are now commonly used in mining operations.
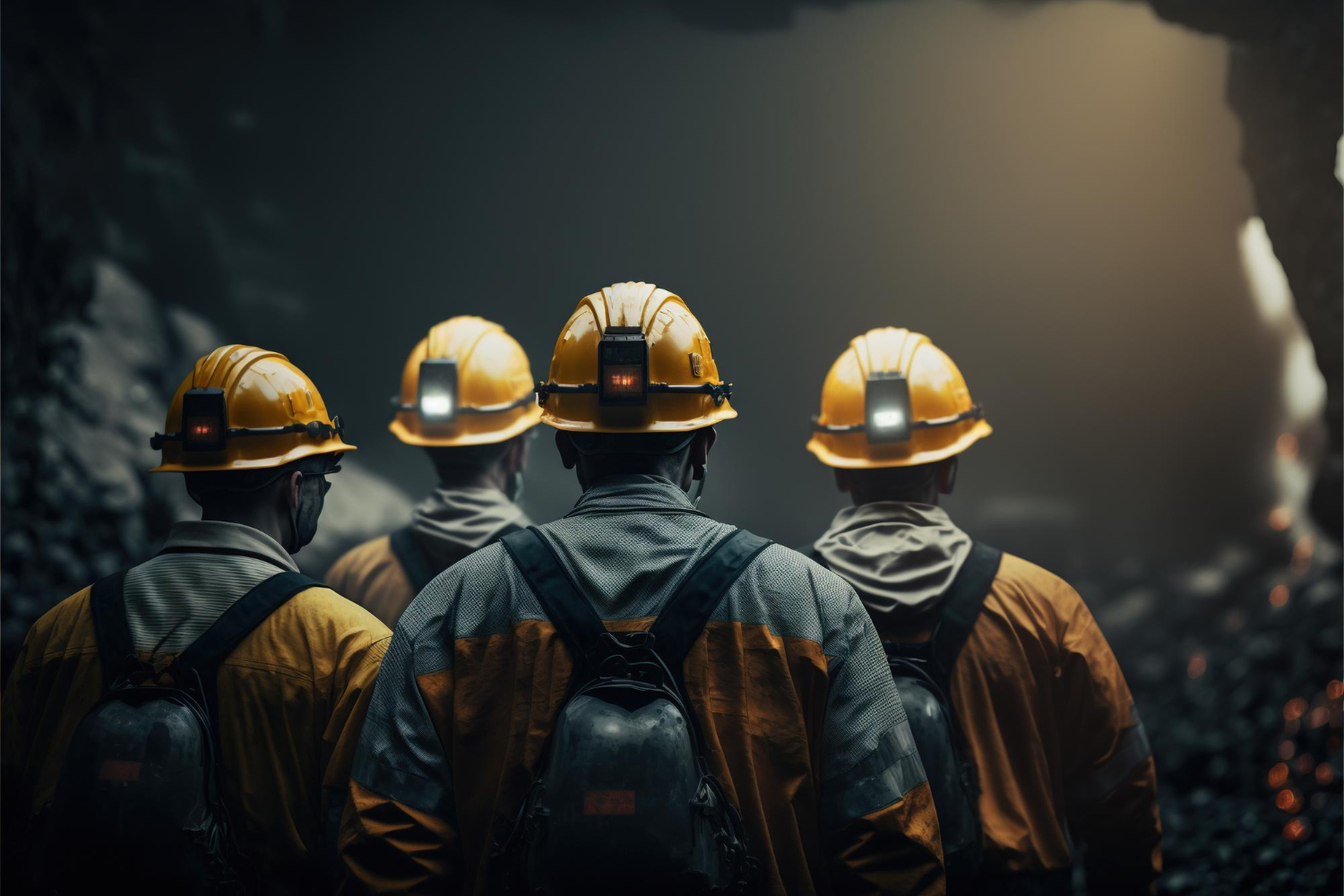
With advancements in sensors, data analytics, and communication technologies, the mining industry has embraced automation to improve efficiency, safety, and productivity. Automated drilling rigs, autonomous haul trucks, and robotic ore sorting systems are just a few examples of how automation has transformed the way mining companies operate. As the industry continues to evolve, we can expect even more cutting-edge automation technologies to be integrated into mining processes, leading to further improvements in safety and operational performance.
The Benefits of Automation for Workforce Safety
Automation in the mining industry has brought significant benefits for workforce safety. By replacing manual labor with automated processes, there is a reduction in the potential for human error, leading to fewer accidents on site. Machines can perform tasks more consistently and precisely than humans, minimizing the risk of injuries and fatalities that may occur due to fatigue or distractions.
Moreover, automation allows for the remote operation of equipment in hazardous environments, keeping workers out of harm’s way. With the use of sensors and real-time monitoring systems, potential safety hazards can be detected early, enabling prompt interventions to prevent accidents. This proactive approach to safety through automation not only protects the workforce but also enhances overall operational efficiency in mining activities.
Challenges Faced in Implementing Automation in Mining
Implementing automation in the mining industry presents several challenges that need to be addressed. One of the primary obstacles is the significant initial investment required to adopt automated systems. The cost of purchasing and implementing the necessary technology can be substantial, making it a barrier for many mining companies, especially smaller operations with limited budgets.
Additionally, integrating automation into existing mining operations can be complex and time-consuming. Companies need to carefully plan and execute the transition to automated systems without disrupting ongoing production activities. This process often requires extensive training for personnel and may involve restructuring certain aspects of the operation to accommodate the new technology seamlessly.
Improvements in Hazard Detection and Prevention Through Automation
Automation has significantly enhanced hazard detection and prevention in the mining industry. Through the utilization of advanced sensors and real-time monitoring systems, potential risks can be identified promptly, allowing for immediate actions to be taken. Additionally, automation enables the collection and analysis of extensive data, facilitating the prediction of potential hazards based on historical patterns and trends.
By integrating automation with artificial intelligence algorithms, mining operations have further improved hazard detection and prevention. These AI systems can recognize patterns in data that may indicate a potential safety issue, providing proactive measures to mitigate risks before accidents occur. Moreover, the utilization of AI allows for continuous learning and adaptation to changing conditions, ensuring that safety protocols remain effective and up-to-date.
Training and Skill Development for Workers in an Automated Mining Environment
Training and skill development for workers in an automated mining environment play a crucial role in ensuring a smooth transition to automated systems. As mining operations adopt more advanced technologies, workers must be equipped with the necessary knowledge and expertise to operate, monitor, and maintain these automated systems effectively. Training programs should focus on enhancing workers’ understanding of the technologies involved, troubleshooting common issues, and emphasizing safety protocols specific to automated mining environments.
Hands-on training sessions are invaluable in providing workers with practical experience in operating automated machinery and systems. Simulated scenarios can help employees become familiar with the intricacies of automated processes, enabling them to respond efficiently to any unexpected challenges they may encounter on the job. Additionally, ongoing skill development programs are essential to keep pace with rapidly evolving technologies in the mining industry, ensuring that workers remain competent and confident in their roles within an increasingly automated environment.
The Role of Artificial Intelligence in Enhancing Workforce Safety
Artificial intelligence (AI) is making significant strides in enhancing workforce safety within the mining industry. By leveraging AI-powered algorithms, mining companies can analyze vast amounts of data to identify potential hazards and proactively mitigate risks before accidents occur. This predictive capability allows for more targeted safety measures and interventions, ultimately reducing the likelihood of injuries or fatalities among workers.
Moreover, AI plays a crucial role in real-time monitoring and decision-making processes, enabling quick responses to emergent safety threats in mining operations. Through the integration of AI technologies with sensor-based systems, companies can detect deviations from safety protocols and automatically trigger alerts or shutdowns when necessary. This rapid intervention not only safeguards the workforce but also contributes to the overall efficiency and productivity of mining activities.
• AI-powered algorithms analyze vast amounts of data to identify potential hazards
• Proactively mitigate risks before accidents occur
• Allows for more targeted safety measures and interventions
• Reduces likelihood of injuries or fatalities among workers
• Real-time monitoring and decision-making processes in mining operations
• Integration of AI technologies with sensor-based systems
• Detect deviations from safety protocols and trigger alerts or shutdowns when necessary
• Safeguards the workforce and contributes to efficiency and productivity
Monitoring and Supervision of Automated Systems in Mining
In the realm of mining operations, the monitoring and supervision of automated systems play a crucial role in ensuring the smooth and efficient functioning of various processes. With the integration of advanced technologies such as sensors and data analytics, monitoring systems can track real-time data on equipment performance, environmental conditions, and worker activities. Supervisory control systems enable operators to remotely monitor operations, identify potential issues, and make prompt adjustments to optimize productivity and safety.
Moreover, the implementation of automated monitoring and supervision systems in mining not only enhances operational efficiency but also contributes significantly to workforce safety. By providing real-time insights into potential hazards and risks, these systems empower operators to take proactive measures to prevent accidents and mitigate risks to personnel. The continuous monitoring of equipment health and environmental conditions allows for early detection of malfunctions or abnormal conditions, thereby improving overall safety standards in mining operations.
Impact of Automation on Reducing Human Error and Accidents
Automation in the mining industry has significantly contributed to reducing human error and accidents. By replacing manual tasks with automated processes, the potential for human oversight or fatigue-related mistakes is greatly minimized. Machines can consistently perform repetitive tasks with precision and accuracy, ensuring a higher level of safety for workers on site. This shift towards automation has led to a notable decrease in incidents caused by human error, ultimately creating a safer working environment in mining operations.
Furthermore, automation systems are equipped with advanced sensors and technologies that can quickly detect potential hazards or deviations from safety protocols. These real-time monitoring capabilities enable automated systems to take immediate corrective actions or alert human operators to intervene before accidents occur. By proactively identifying risks and implementing preventive measures, automation plays a crucial role in mitigating safety hazards and reducing the likelihood of accidents in mining operations.
Integration of Automation with Existing Safety Protocols in Mining
Automation is revolutionizing the mining industry by augmenting existing safety protocols to enhance workforce safety. By seamlessly integrating automated systems with established safety measures, mining operations can achieve higher levels of efficiency and risk mitigation. This collaborative approach ensures that automation complements and strengthens the safety practices already in place, rather than replacing them entirely.
The synchronization of automation with existing safety protocols requires careful planning, coordination, and monitoring. Mining companies must conduct thorough assessments to identify areas where automation can supplement safety measures effectively. By aligning automated processes with established protocols, the industry can cultivate a culture of safety that prioritizes the well-being of workers while optimizing operational performance.
Addressing Concerns about Job Displacement Due to Automation
Mining industry is no stranger to concerns about job displacement due to the increasing adoption of automation. As more tasks traditionally performed by human workers are being taken over by machines and AI systems, there is a valid worry about the future of jobs in this sector. However, it’s important to note that while automation may lead to some job roles becoming obsolete, it also creates new opportunities for roles that require different skills, such as maintenance and programming of automated systems.
One way to address concerns about job displacement is through proactive workforce planning and retraining programs. By investing in upskilling and reskilling initiatives for workers affected by automation, mining companies can help employees transition into new roles that align with the evolving needs of the industry. Additionally, fostering a culture of continuous learning and adaptability within the workforce can empower employees to embrace change and stay relevant in a more automated mining environment.
Regulatory Compliance and Safety Standards in Automated Mining Operations
Mining operations that integrate automation technologies must adhere to stringent regulatory compliance and safety standards to ensure the well-being of workers and the surrounding environment. These standards are essential to minimize risks associated with automated systems, such as equipment malfunctions or human errors that could potentially result in accidents. By following established guidelines and regulations, mining companies can proactively address safety concerns and maintain a secure working environment for their employees.
Implementing automation in mining operations requires a comprehensive understanding and adherence to safety protocols set forth by regulatory authorities. Compliance with these standards not only safeguards the workforce but also contributes to the overall efficiency and productivity of the operation. By prioritizing safety measures and compliance with regulations, mining companies can mitigate potential risks and optimize the benefits of automation technologies in the industry.
Future Outlook for Automation and Workforce Safety in Mining
The future outlook for automation and workforce safety in the mining industry appears promising as technological advancements continue to drive innovation. With the integration of artificial intelligence and advanced sensors, mining operations can achieve higher levels of safety and efficiency. Companies are increasingly investing in automation solutions to enhance workplace safety, reduce human error, and improve overall productivity.
As we look ahead, the seamless integration of automation with existing safety protocols will be critical in ensuring a smooth transition towards a safer working environment in mines. Training programs tailored to equip workers with the necessary skills to operate and supervise automated systems will play a pivotal role in enhancing workforce safety. By addressing concerns about job displacement through strategic planning and retraining initiatives, the mining industry can capitalize on the potential of automation while prioritizing the safety and well-being of its workforce.
Case Studies Highlighting Successful Implementation of Automation for Safety in Mining Operations
One notable case study showcasing the successful implementation of automation for safety in the mining industry is at XYZ Mining Company. By integrating automated systems for monitoring hazardous conditions and providing real-time alerts to workers, the company has significantly reduced the risks associated with potential accidents. This proactive approach to safety has not only improved the well-being of the workforce but has also enhanced overall operational efficiency.
In another case study at ABC Mining Corporation, the utilization of automation in equipment maintenance has revolutionized safety protocols. Through predictive maintenance algorithms, the company can preemptively detect potential issues before they escalate, thereby preventing unplanned downtime and hazardous situations. The implementation of automation in maintenance procedures has not only ensured the continuous operation of machinery but has also created a safer working environment for all personnel involved.
Additional Resources:
Table of Contents
- The Evolution of Automation in the Mining Industry
- The Benefits of Automation for Workforce Safety
- Challenges Faced in Implementing Automation in Mining
- Improvements in Hazard Detection and Prevention Through Automation
- Training and Skill Development for Workers in an Automated Mining Environment
- The Role of Artificial Intelligence in Enhancing Workforce Safety
- Monitoring and Supervision of Automated Systems in Mining
- Impact of Automation on Reducing Human Error and Accidents
- Integration of Automation with Existing Safety Protocols in Mining
- Addressing Concerns about Job Displacement Due to Automation
- Regulatory Compliance and Safety Standards in Automated Mining Operations
- Future Outlook for Automation and Workforce Safety in Mining
- Case Studies Highlighting Successful Implementation of Automation for Safety in Mining Operations
- Additional Resources:
- FAQs:
- What are some of the benefits of implementing automation in mining operations for workforce safety?
- What are some challenges faced in implementing automation in the mining industry?
- How can artificial intelligence help enhance workforce safety in mining operations?
- How can automation be integrated with existing safety protocols in mining operations?
- What is the future outlook for automation and workforce safety in the mining industry?
Catetgories:
- AI
- AI, IIoT
- AI, Machine Learning
- AI, Robotics
- Automation
- Automation, AI
- Automation, Data Analytics
- Automation, Drones
- Big Data
- Blockchain
- Digital Transformation
- Digital Twins
- Drones
- Edge Computing
- IIoT
- IIoT
- IIoT
- IIoT
- IIoT
- IIoT, Cloud Computing
- IIoT, Machine Learning
- IIoT, Robotics
- IoT
- Machine Learning
- Mining 4.0
- Mining 4.0, AI
- Mining 4.0, AI, IIoT
- Mining 4.0, IIoT
- Mining 4.0, Robotics
- Pit to Port Automation
- Predictive Maintenance
- Smart Mining
- Uncategorized
- Virtual Reality
Latest Posts:
[sbs_latest_posts]
FAQs:
What are some of the benefits of implementing automation in mining operations for workforce safety?
Automation in mining operations can lead to improved hazard detection and prevention, reduced human error and accidents, and enhanced monitoring and supervision of systems to ensure a safer working environment for workers.
What are some challenges faced in implementing automation in the mining industry?
Some challenges include the initial investment costs, training and skill development for workers to adapt to automated systems, and concerns about job displacement due to automation.
How can artificial intelligence help enhance workforce safety in mining operations?
Artificial intelligence can improve hazard detection and prediction, optimize workflows for better safety outcomes, and enable quicker responses to potential safety risks in mining operations.
How can automation be integrated with existing safety protocols in mining operations?
Automation can be integrated with existing safety protocols by ensuring that automated systems align with regulatory compliance and safety standards, and by providing proper training and supervision for workers to use automated systems effectively.
What is the future outlook for automation and workforce safety in the mining industry?
The future of automation in mining operations is expected to continue to evolve, with a focus on improving safety measures, reducing accidents, and enhancing overall efficiency in the industry.