The Benefits of Automation in Improving Mine Site Safety
Automation technology has revolutionized the mining industry by significantly improving mine site safety. By replacing manual labor with automated systems, the risk of human error and accidents is greatly reduced. Automated equipment and machinery can perform tasks with precision and consistency, minimizing the potential for workplace hazards.
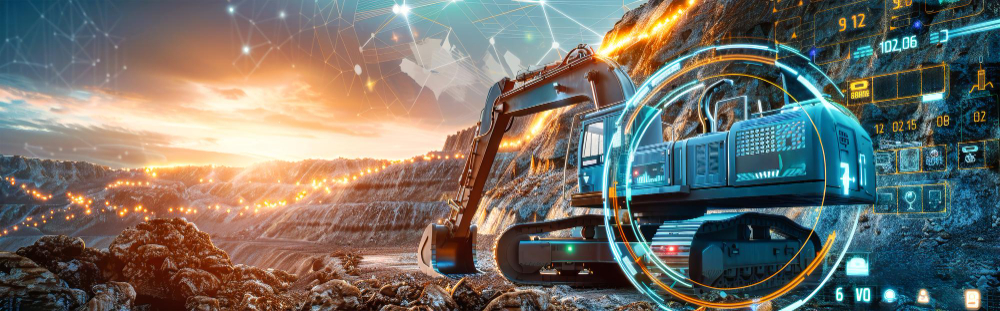
Furthermore, automation solutions enable real-time data analysis, providing valuable insights into safety measures and potential risks. With the ability to monitor operations continuously, mine managers can quickly identify and address safety concerns before they escalate. Overall, the implementation of automation technology in mining operations has proven to be instrumental in creating a safer working environment for all personnel involved.
How Automation Technology Can Help Prevent Accidents
Automation technology plays a crucial role in preventing accidents at mine sites by minimizing the need for human intervention in high-risk tasks. By utilizing automated equipment and machinery, companies can reduce the exposure of workers to hazardous environments, ultimately decreasing the likelihood of accidents occurring. With the integration of robotics and autonomous vehicles into daily operations, the reliance on human decision-making in dangerous situations is significantly reduced, enhancing overall safety protocols.
In addition to reducing the risk of accidents, automation technology enables real-time monitoring and data analysis, providing valuable insights into potential safety hazards. By utilizing drones for efficient monitoring and inspection, companies can identify safety issues before they escalate into accidents, allowing for proactive measures to be implemented promptly. The utilization of AI for predictive maintenance further enhances safety measures by enabling early detection of equipment malfunctions, preventing potential accidents due to equipment failures.
Enhancing Productivity Through Automation Solutions
Automation solutions play a pivotal role in boosting productivity within mining operations. By automating repetitive tasks and streamlining processes, companies can increase efficiency and output. This not only saves time but also reduces the likelihood of human errors, leading to a more consistent and reliable workflow.
Moreover, automation allows mining companies to optimize resource allocation and enhance overall operational performance. With real-time monitoring and data analysis capabilities, decision-makers can make informed choices promptly, leading to improved productivity levels. By embracing automation solutions, mine sites can achieve higher production rates while maintaining stringent safety standards.
• Automation solutions streamline processes and automate repetitive tasks
• Increases efficiency and output within mining operations
• Reduces the likelihood of human errors for a more consistent workflow
• Optimizes resource allocation and enhances operational performance
• Real-time monitoring and data analysis capabilities aid in informed decision-making
• Helps achieve higher production rates while maintaining safety standards
The Role of Robotics in Minimizing Human Error
Robots play a crucial role in minimizing human error in various industries, including mining. By automating repetitive and potentially dangerous tasks, robots can significantly reduce the risk of accidents caused by human mistakes. With their precision and accuracy, robots can perform tasks with consistent quality, eliminating the variability that can result from human involvement.
In addition to improving safety, robotics can also enhance productivity by streamlining processes and increasing efficiency. By handling tasks that are better suited for automation, robots free up human workers to focus on more complex and strategic aspects of their work. This not only reduces the chances of errors but also allows for a more streamlined and productive workflow in mining operations.
Implementing Autonomous Vehicles for Safer Mine Operations
Autonomous vehicles have emerged as a game-changer in the mining industry, offering a safer alternative to traditional manned vehicles. These advanced vehicles are equipped with sensors and artificial intelligence algorithms that enable them to navigate through the mine site autonomously, reducing the risk of accidents caused by human error. By removing the need for human drivers in hazardous environments, autonomous vehicles can effectively minimize the potential for workplace injuries and fatalities, making mine operations significantly safer.
Moreover, implementing autonomous vehicles in mine operations can also lead to increased efficiency and productivity. These vehicles can operate around the clock without the need for breaks, ensuring continuous workflow and optimal utilization of resources. By streamlining transportation and logistics processes, autonomous vehicles can help mine sites meet production targets more effectively, ultimately contributing to a more profitable operation.
Utilizing Drones for Efficient Monitoring and Inspection
Drones have revolutionized the way mine sites are monitored and inspected, offering a cost-effective and efficient solution to enhance safety and productivity. Equipped with high-resolution cameras and sensors, drones can navigate through challenging terrain to provide real-time data on various aspects of the site. This data can be used for assessing equipment performance, identifying potential hazards, and conducting accurate inspections without putting human workers at risk.
Furthermore, the use of drones enables mine operators to cover large areas in a shorter amount of time compared to traditional inspection methods. By capturing detailed imagery and videos, drones allow for in-depth analysis of the site, leading to informed decision-making and proactive maintenance strategies. The ability to access remote or hazardous areas easily makes drones an invaluable tool in improving overall safety measures and ensuring regulatory compliance within the mining industry.
The Advantages of Real-time Data Analysis in Enhancing Safety Measures
Real-time data analysis plays a crucial role in enhancing safety measures within mine sites. By continuously monitoring data streams from various sensors and equipment, potential hazards can be quickly identified and addressed before they escalate into dangerous situations. This proactive approach allows for timely interventions and preventative actions to be taken, ultimately reducing the risk of accidents and ensuring a safer working environment for miners.
Moreover, real-time data analysis enables mine operators to gain valuable insights into operational trends and patterns that may impact safety. By analyzing historical data alongside current information, trends can be identified and predictive models can be developed to forecast potential safety risks. This foresight allows for proactive decision-making and the implementation of targeted safety measures to prevent accidents and prioritize the well-being of all personnel on site.
Optimizing Workflows with Automated Equipment and Machinery
Automation has revolutionized the mining industry by streamlining workflows with the use of advanced equipment and machinery. This technology has significantly improved efficiency and productivity in various operations within mine sites. Automated systems can handle tasks with precision and speed, reducing the potential for errors and delays.
The integration of automated equipment and machinery has also led to smoother coordination between different processes in mining operations. With tasks being performed seamlessly and accurately, the overall workflow becomes more structured and optimized. This not only enhances productivity but also enhances safety measures by minimizing the risks associated with manual labor.
Reducing Workplace Hazards with Remote Control Systems
Remote control systems play a crucial role in reducing workplace hazards by allowing operators to oversee operations from a safe distance. This enables personnel to control machinery and equipment in potentially hazardous environments without exposing themselves to danger. By operating equipment remotely, workers can navigate through challenging terrains or handle risky materials while maintaining a safe distance, minimizing the risk of accidents and injuries on the job.
Moreover, remote control systems offer increased precision and accuracy in managing tasks, leading to improved safety outcomes. Operators can manipulate equipment with finesse and efficiency, reducing the likelihood of errors or malfunctions. With the ability to operate machinery from afar, workers can focus on executing tasks with heightened attention to detail, ensuring that operations run smoothly and without incident.
Integrating Artificial Intelligence for Predictive Maintenance
Artificial intelligence (AI) is revolutionizing the mining industry by enabling predictive maintenance strategies that help prevent costly equipment breakdowns. By utilizing AI algorithms to analyze data from sensors and machine learning models, mining companies can forecast potential issues before they occur, allowing for timely maintenance interventions. This proactive approach not only reduces downtime and maintenance costs but also enhances operational efficiency and equipment lifespan.
The integration of AI for predictive maintenance in mining operations ensures that maintenance tasks are carried out based on real-time equipment condition data rather than fixed schedules. This targeted maintenance approach maximizes equipment uptime and minimizes the risk of unexpected failures, improving overall mine site safety and productivity. As AI continues to advance, mining companies can expect even more sophisticated predictive maintenance capabilities that will further optimize maintenance schedules and drive continuous improvements in operational performance.
Maximizing Efficiency with Automated Inventory Management
Automated inventory management systems have revolutionized the way mining operations handle their stock levels. By utilizing technology to track, manage, and optimize inventory, companies can streamline their processes and ensure that the right materials are available when needed. These systems eliminate the need for manual tracking and minimize the chance of human error in inventory management, ultimately leading to improved efficiency and cost savings.
Moreover, automated inventory management facilitates real-time monitoring of stock levels, enabling mining companies to make informed decisions quickly. With the ability to set up automatic alerts for low stock or overstock situations, organizations can avoid costly delays or disruptions in their operations. By implementing these automated systems, mines can maximize efficiency in their inventory management, ultimately contributing to overall productivity and profitability.
Enhancing Communication and Coordination Through Automation
Effective communication and coordination are essential elements in ensuring smooth and safe operations at mine sites. Automation technology plays a crucial role in enhancing these aspects by providing real-time data sharing capabilities among different teams and departments. By automating communication channels through centralized systems, stakeholders can receive critical updates and instructions promptly, enabling quick decision-making and response to any potential issues or emergencies that may arise.
Furthermore, automation also aids in streamlining coordination efforts by facilitating task assignments, scheduling, and resource allocation. Through integrated automation solutions, mine site managers can optimize workflows and allocate resources more efficiently, leading to improved productivity and operational efficiency. By leveraging automation for communication and coordination purposes, mining companies can enhance overall safety measures and maximize productivity levels at their sites.
The Future of Mine Site Safety and Productivity with Automation Technology
Automation technology is revolutionizing the way mining operations are carried out, with a strong focus on enhancing safety protocols and increasing productivity. By incorporating automated solutions such as robotics, autonomous vehicles, and drones, mine sites can minimize human error, reduce workplace hazards, and efficiently monitor and inspect operations. Real-time data analysis plays a crucial role in enabling quick decision-making and implementing proactive safety measures, ultimately leading to a safer and more efficient working environment.
The integration of artificial intelligence for predictive maintenance and automated inventory management further optimizes workflows and maximizes efficiency in mine operations. Remote control systems enable operators to oversee tasks from a safe distance, reducing the risks associated with manual labor. In addition, automation technology enhances communication and coordination among team members, ensuring seamless collaboration and effective resource management. As mining companies continue to invest in automation solutions, the future of mine site safety and productivity looks promising, with technology playing a pivotal role in driving sustainable and efficient practices.
Additional Rsources:
- The Impact of Automation on Mine Site Safety and Productivity
- The Impact of Automation on Mining Sustainability
- The Future of Autonomous Vehicles in Mining
- The Future of Drilling Automation in Mining
- Automation in Mining: Overcoming Implementation Challenges
- Automation in Mineral Exploration: Benefits and Challenges
- Advancements in Autonomous Mining Vehicles
- Automation in Mining: Reducing Human Error and Increasing Precision
- Automated Exploration: Innovations in Mining Technology
- The Future of Mining Operations with Automation
Table of Contents
- The Benefits of Automation in Improving Mine Site Safety
- How Automation Technology Can Help Prevent Accidents
- Enhancing Productivity Through Automation Solutions
- The Role of Robotics in Minimizing Human Error
- Implementing Autonomous Vehicles for Safer Mine Operations
- Utilizing Drones for Efficient Monitoring and Inspection
- The Advantages of Real-time Data Analysis in Enhancing Safety Measures
- Optimizing Workflows with Automated Equipment and Machinery
- Reducing Workplace Hazards with Remote Control Systems
- Integrating Artificial Intelligence for Predictive Maintenance
- Maximizing Efficiency with Automated Inventory Management
- Enhancing Communication and Coordination Through Automation
- The Future of Mine Site Safety and Productivity with Automation Technology
- Additional Rsources:
- FAQs:
- How can automation technology improve mine site safety?
- How does automation technology enhance productivity in mining operations?
- What role do robotics play in minimizing human error at mine sites?
- How can autonomous vehicles contribute to safer mine operations?
- What are the benefits of utilizing drones for monitoring and inspection at mine sites?
- How can real-time data analysis improve safety measures at mine sites?
- What are the advantages of implementing remote control systems for mining operations?
- How can artificial intelligence be used for predictive maintenance in mining operations?
- How does automated inventory management maximize efficiency at mine sites?
- What is the future of mine site safety and productivity with automation technology?
Categories:
- AI
- AI, IIoT
- AI, Machine Learning
- AI, Robotics
- Automation
- Automation, AI
- Automation, Data Analytics
- Automation, Drones
- Big Data
- Blockchain
- Digital Transformation
- Digital Twins
- Drones
- Edge Computing
- IIoT
- IIoT
- IIoT
- IIoT
- IIoT
- IIoT, Cloud Computing
- IIoT, Machine Learning
- IIoT, Robotics
- IoT
- Machine Learning
- Mining 4.0
- Mining 4.0, AI
- Mining 4.0, AI, IIoT
- Mining 4.0, IIoT
- Mining 4.0, Robotics
- Pit to Port Automation
- Predictive Maintenance
- Smart Mining
- Uncategorized
- Virtual Reality
Latest Posts:
[sbs_latest_posts]
FAQs:
How can automation technology improve mine site safety?
Automation technology can improve mine site safety by reducing the risk of accidents through the use of autonomous vehicles, drones for monitoring, real-time data analysis for safety measures, and remote control systems to minimize workplace hazards.
How does automation technology enhance productivity in mining operations?
Automation technology enhances productivity by optimizing workflows with automated equipment and machinery, integrating artificial intelligence for predictive maintenance, maximizing efficiency with automated inventory management, and improving communication and coordination through automation.
What role do robotics play in minimizing human error at mine sites?
Robotics can minimize human error at mine sites by performing tasks with precision and accuracy, reducing the likelihood of accidents and improving overall safety measures.
How can autonomous vehicles contribute to safer mine operations?
Autonomous vehicles can contribute to safer mine operations by eliminating the need for human operators in hazardous environments, reducing the risk of accidents and injuries.
What are the benefits of utilizing drones for monitoring and inspection at mine sites?
Drones can provide efficient monitoring and inspection of mine sites, allowing for real-time data collection and analysis, as well as identifying potential safety hazards from a safe distance.
How can real-time data analysis improve safety measures at mine sites?
Real-time data analysis can improve safety measures at mine sites by providing immediate insights into potential risks and hazards, allowing for proactive measures to be taken to prevent accidents.
What are the advantages of implementing remote control systems for mining operations?
Remote control systems can help reduce workplace hazards by allowing operators to control equipment and machinery from a safe distance, minimizing the risk of accidents and injuries.
How can artificial intelligence be used for predictive maintenance in mining operations?
Artificial intelligence can be used for predictive maintenance in mining operations by analyzing data to predict when equipment is likely to fail, allowing for proactive maintenance to be conducted to prevent downtime and accidents.
How does automated inventory management maximize efficiency at mine sites?
Automated inventory management maximizes efficiency by streamlining the process of tracking and managing inventory, reducing the risk of stockouts and ensuring that operations run smoothly.
What is the future of mine site safety and productivity with automation technology?
The future of mine site safety and productivity with automation technology is promising, with advancements in robotics, autonomous vehicles, drones, real-time data analysis, and artificial intelligence expected to further improve safety measures and enhance productivity in mining operations.