The Importance of Predictive Maintenance in the Mining Industry
Predictive maintenance is crucial for the mining industry as it helps mining companies prevent costly equipment failures by identifying potential issues before they escalate. By leveraging data and analytics, mining companies can schedule maintenance proactively based on the actual condition of the equipment, reducing unplanned downtime and maximizing production output. This approach not only saves time and resources but also increases safety for workers by minimizing the risk of sudden equipment malfunctions in hazardous mining environments.
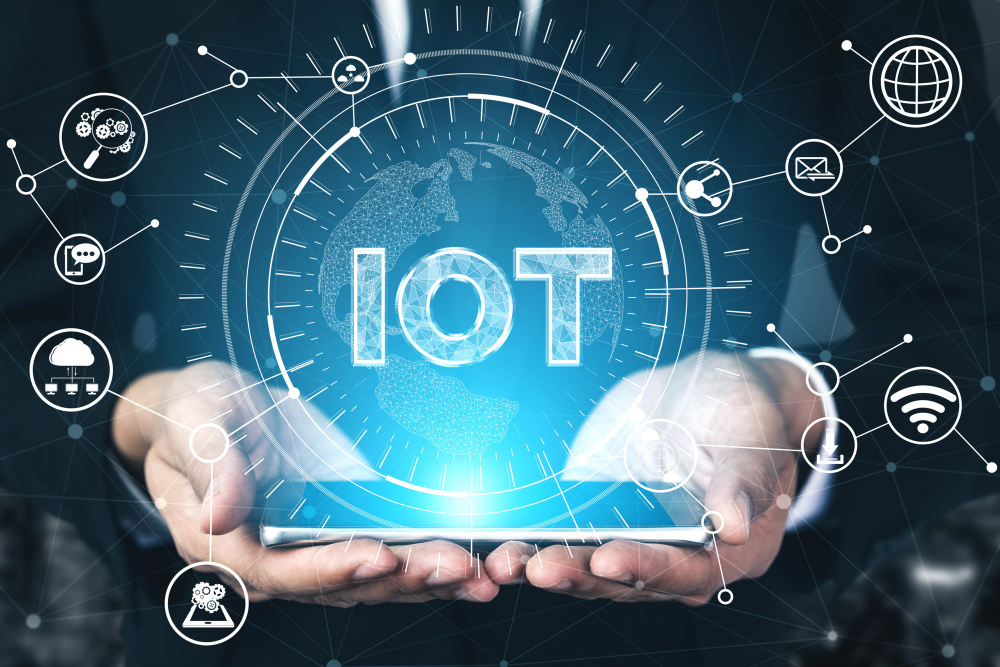
In addition to cost savings and improved safety, predictive maintenance also contributes to extending the lifespan of mining equipment. By monitoring the health of equipment components in real-time and detecting abnormalities early on, companies can address underlying issues promptly, ultimately prolonging the operational life of assets and optimizing their performance. This proactive maintenance strategy enables mining companies to increase equipment reliability and efficiency, leading to enhanced operational effectiveness and sustained profitability in the long run.
Challenges Faced by Mining Companies in Maintaining Equipment
Mining companies face a myriad of challenges when it comes to maintaining equipment in their operations. One of the major obstacles is the harsh and demanding environment in which mining equipment operates. The constant exposure to dust, dirt, moisture, and extreme temperatures can lead to accelerated wear and tear, requiring frequent maintenance and repairs to ensure optimal performance. Additionally, the sheer size and complexity of mining machinery make it difficult to keep track of all components and anticipate potential failures.
Another significant challenge is the high cost associated with maintaining mining equipment. From regular inspections and routine maintenance to unexpected breakdowns and replacements, the financial burden of keeping equipment operational can be substantial. Limited budgets and resources further compound this issue, forcing mining companies to prioritize maintenance activities and sometimes resort to reactive rather than proactive maintenance practices. These challenges highlight the need for effective predictive maintenance strategies to help mining companies overcome these obstacles and improve equipment reliability and performance.
Benefits of Extending the Lifespan of Mining Equipment
Extending the lifespan of mining equipment can lead to significant cost savings for mining companies. By reducing the frequency of equipment replacements, companies can lower their capital expenditures and improve overall budget management. This also helps in minimizing downtime due to maintenance or replacement activities, allowing mining operations to run smoothly and continuously, thereby maximizing productivity.
Moreover, extending the lifespan of mining equipment can enhance operational efficiency. When equipment is well-maintained and in good working condition, it can operate at optimal levels, ensuring that production targets are consistently met. This not only boosts operational output but also contributes to a more sustainable and environmentally friendly approach, as fewer resources are consumed in the manufacturing and disposal of equipment components.
How IIoT Technology is Revolutionizing Predictive Maintenance
IIoT technology, also known as the Industrial Internet of Things, is transforming the landscape of predictive maintenance in the mining industry. By enabling real-time monitoring and data collection from sensors installed on mining equipment, IIoT technology provides crucial insights into the health and performance of machinery. This continuous stream of data allows maintenance teams to detect potential issues before they escalate, leading to more efficient and proactive maintenance strategies.
Moreover, IIoT technology facilitates remote monitoring of equipment, eliminating the need for manual inspections and intervention. With the ability to analyze vast amounts of data in a timely manner, mining companies can optimize their maintenance schedules, reduce downtime, and ultimately prolong the lifespan of their equipment. This shift towards predictive maintenance driven by IIoT technology not only enhances the reliability of mining operations but also contributes to cost savings and improved overall productivity.
Key Components of an Effective Predictive Maintenance Strategy
When developing an effective predictive maintenance strategy for mining equipment, several key components must be considered. Firstly, a comprehensive data collection system is crucial. This involves gathering real-time data from sensors and devices installed on the equipment to monitor its performance continuously. The data collected should be stored securely and analyzed to identify patterns or anomalies that could indicate potential issues.
Secondly, having a robust predictive maintenance scheduling system is essential. This includes setting up alerts and notifications based on the data analysis to prompt maintenance activities proactively. By using predictive algorithms to anticipate when equipment is likely to require servicing or parts replacement, downtime can be minimized, and overall operational efficiency improved. Integrating these components into a coherent strategy can significantly enhance the reliability and lifespan of mining equipment, ultimately leading to cost savings and increased productivity.
The Role of Data Analytics in Predictive Maintenance for Mining Equipment
Data analytics plays a crucial role in enhancing predictive maintenance strategies for mining equipment. By analyzing large sets of data collected from sensors and other sources, mining companies can gain valuable insights into the health and performance of their equipment. This allows them to predict potential failures before they occur, leading to reduced downtime and cost savings.
Furthermore, data analytics helps in identifying patterns and trends in equipment behavior, enabling mining companies to optimize maintenance schedules and reduce unnecessary maintenance activities. With the power of data analytics, mining operators can make informed decisions, ultimately improving operational efficiency and extending the lifespan of their equipment.
• Data analytics allows mining companies to analyze large sets of data from sensors and other sources
• Predict potential failures before they occur, reducing downtime and cost savings
• Identify patterns and trends in equipment behavior for optimized maintenance schedules
• Reduce unnecessary maintenance activities with insights from data analytics
• Make informed decisions to improve operational efficiency and extend equipment lifespan
Case Studies: Successful Implementation of Predictive Maintenance in Mining
In one case study, a large mining company implemented a predictive maintenance program that significantly reduced downtime and maintenance costs for their fleet of heavy equipment. By utilizing advanced sensors and data analytics, the company was able to accurately predict when components needed servicing or replacement, allowing them to proactively address issues before they led to costly breakdowns. As a result, the company saw a notable increase in equipment reliability and operational efficiency, ultimately leading to improved productivity and profitability.
Another successful implementation of predictive maintenance in the mining industry involved a mid-sized operation that struggled with unplanned equipment failures and high maintenance expenses. After adopting a predictive maintenance approach that leveraged real-time monitoring and machine learning algorithms, the company experienced a dramatic shift in their maintenance strategy. By identifying patterns in equipment performance and implementing proactive maintenance measures, the company not only reduced unplanned downtime but also extended the lifespan of their equipment. This resulted in significant cost savings and improved overall equipment effectiveness for the mining operation.
Common Predictive Maintenance Techniques Used in the Mining Sector
An essential element of predictive maintenance in the mining sector is vibration analysis. By monitoring the vibrations of mining equipment like crushers, pumps, and conveyors, maintenance teams can detect potential issues such as misalignments, bearing failures, or structural defects before they lead to costly breakdowns. Regular vibration analysis allows for timely repairs and adjustments, minimizing downtime and extending the lifespan of the equipment.
Another common predictive maintenance technique used in the mining industry is oil analysis. By regularly sampling and analyzing the oil used in heavy machinery such as excavators and haul trucks, maintenance teams can identify contaminants, wear particles, and other indicators of potential problems. Oil analysis helps in detecting issues like component wear, lubricant degradation, and fluid leaks, enabling proactive maintenance actions to prevent equipment failures and ensure optimal performance.
Ensuring Safety and Compliance Through Predictive Maintenance
Predictive maintenance plays a crucial role in ensuring the safety and compliance of mining operations. By proactively monitoring the condition of equipment, potential hazards can be identified and addressed before they escalate into serious safety risks. This proactive approach not only helps in preventing accidents but also ensures that mining companies comply with the stringent regulations and standards set by governing bodies.
In addition, predictive maintenance can contribute to maintaining a safe working environment by minimizing unexpected equipment failures that could pose risks to workers. By continuously monitoring the health of machinery and identifying areas that require attention, mining companies can effectively plan maintenance activities to prevent any potential safety issues. This proactive maintenance approach not only enhances safety protocols but also helps in maintaining compliance with industry regulations related to the safety of the work environment.
Maximizing Efficiency and Productivity with Predictive Maintenance
In the mining industry, maximizing efficiency and productivity are crucial for maintaining a competitive edge. Predictive maintenance plays a pivotal role in achieving these goals by proactively identifying potential equipment issues before they escalate into costly downtimes. By implementing predictive maintenance strategies, mining companies can schedule maintenance activities during planned downtime, minimizing disruptions to operations and optimizing equipment performance.
Furthermore, predictive maintenance enables mining companies to shift from reactive to proactive maintenance practices. By leveraging data-driven insights and real-time monitoring, maintenance activities can be tailored to the specific needs of each piece of equipment, ultimately enhancing reliability and extending the lifespan of assets. This proactive approach not only improves overall equipment effectiveness but also contributes to a safer working environment for personnel.
Future Trends in IIoT and Predictive Maintenance for Mining Equipment
The future of the mining industry is intertwined with the continuous advancement of Industrial Internet of Things (IIoT) technology and predictive maintenance practices. As mining companies strive to enhance operational efficiency and reduce downtime, the utilization of IIoT sensors and data analytics will play an increasingly pivotal role in predictive maintenance strategies. The ability to collect real-time data from mining equipment enables proactive monitoring and timely intervention, leading to significant cost savings and optimized equipment performance.
Moreover, the integration of artificial intelligence and machine learning algorithms into predictive maintenance systems is poised to revolutionize how mining companies manage their equipment. These technologies have the capability to analyze vast amounts of machine data, detect anomalies, and predict potential failures before they occur. By harnessing the power of IIoT and predictive maintenance, mining companies can not only prolong the lifespan of their equipment but also boost productivity and ensure safer working environments for their personnel.
Training and Skill Development for Implementing Predictive Maintenance Programs
To successfully implement predictive maintenance programs in the mining industry, training and skill development are crucial aspects that cannot be overlooked. Mining companies must invest in providing comprehensive training for their maintenance teams to ensure they have the necessary knowledge and expertise to effectively utilize predictive maintenance tools and techniques. This training should cover a wide range of topics, including data analysis, equipment diagnostics, sensor technologies, and maintenance best practices.
Moreover, ongoing skill development is essential to keep maintenance teams up-to-date with the latest advancements in predictive maintenance technologies and methodologies. By providing continuous learning opportunities, mining companies can empower their employees to enhance their skills and stay ahead of the curve in implementing predictive maintenance programs. This focus on training and skill development not only improves the efficiency and effectiveness of maintenance operations but also contributes to the overall success and profitability of mining operations.
Measuring the ROI of Predictive Maintenance Initiatives in Mining Industry
Predictive maintenance initiatives in the mining industry can yield significant returns on investment (ROI) when effectively implemented. By utilizing real-time data and advanced analytics, mining companies can optimize their maintenance schedules, reduce equipment downtime, and ultimately increase productivity. The ability to proactively address potential equipment failures before they occur not only enhances operational efficiency but also helps in avoiding costly repairs and replacements.
Measuring the ROI of predictive maintenance programs involves assessing various factors such as the reduction in unplanned downtime, increased equipment lifespan, and improved overall equipment effectiveness (OEE). By quantifying the financial savings and operational benefits generated through predictive maintenance, mining companies can determine the effectiveness of their initiatives and make informed decisions on resource allocation and future investments in maintenance strategies. Ultimately, a thorough evaluation of ROI enables mining companies to continuously refine and enhance their predictive maintenance programs for ongoing improvements in performance and profitability.
Additional Resources:
- IIoT and Predictive Maintenance: Extending the Lifespan of Mining Equipment
- IIoT and Blockchain: Enhancing Transparency in Mining Operations
- IIoT and Smart Sensors: Revolutionizing Mining Operations
- The Impact of IIoT on Mining Equipment Maintenance
- IIoT and Predictive Analytics in Mining
- IIoT and Safety: Creating a Safer Mining Environment
Table of Contents
- The Importance of Predictive Maintenance in the Mining Industry
- Challenges Faced by Mining Companies in Maintaining Equipment
- Benefits of Extending the Lifespan of Mining Equipment
- How IIoT Technology is Revolutionizing Predictive Maintenance
- Key Components of an Effective Predictive Maintenance Strategy
- The Role of Data Analytics in Predictive Maintenance for Mining Equipment
- Case Studies: Successful Implementation of Predictive Maintenance in Mining
- Common Predictive Maintenance Techniques Used in the Mining Sector
- Ensuring Safety and Compliance Through Predictive Maintenance
- Maximizing Efficiency and Productivity with Predictive Maintenance
- Future Trends in IIoT and Predictive Maintenance for Mining Equipment
- Training and Skill Development for Implementing Predictive Maintenance Programs
- Measuring the ROI of Predictive Maintenance Initiatives in Mining Industry
- Additional Resources:
- FAQs:
- What is the importance of predictive maintenance in the mining industry?
- What are some common challenges faced by mining companies in maintaining equipment?
- How can extending the lifespan of mining equipment benefit companies?
- How is IIoT technology revolutionizing predictive maintenance in the mining industry?
- What are the key components of an effective predictive maintenance strategy?
- How does data analytics play a role in predictive maintenance for mining equipment?
- What are some common predictive maintenance techniques used in the mining sector?
- How can predictive maintenance help ensure safety and compliance in the mining industry?
- How can predictive maintenance help maximize efficiency and productivity in mining operations?
- What are some future trends in IIoT and predictive maintenance for mining equipment?
- How important is training and skill development for implementing predictive maintenance programs in the mining industry?
- How can companies measure the ROI of their predictive maintenance initiatives in the mining industry?
Categories:
- AI
- AI, IIoT
- AI, Machine Learning
- AI, Robotics
- Automation
- Automation, AI
- Automation, Data Analytics
- Automation, Drones
- Big Data
- Blockchain
- Digital Transformation
- Digital Twins
- Drones
- Edge Computing
- IIoT
- IIoT
- IIoT
- IIoT
- IIoT
- IIoT, Cloud Computing
- IIoT, Machine Learning
- IIoT, Robotics
- IoT
- Machine Learning
- Mining 4.0
- Mining 4.0, AI
- Mining 4.0, AI, IIoT
- Mining 4.0, IIoT
- Mining 4.0, Robotics
- Pit to Port Automation
- Predictive Maintenance
- Smart Mining
- Uncategorized
- Virtual Reality
Latest Posts:
[sbs_latest_posts]
FAQs:
What is the importance of predictive maintenance in the mining industry?
Predictive maintenance helps mining companies avoid costly breakdowns, reduce downtime, and extend the lifespan of equipment.
What are some common challenges faced by mining companies in maintaining equipment?
Mining companies often struggle with aging equipment, remote locations, harsh operating conditions, and the high cost of maintenance and repairs.
How can extending the lifespan of mining equipment benefit companies?
Extending the lifespan of mining equipment can lead to cost savings, increased productivity, improved safety, and reduced environmental impact.
How is IIoT technology revolutionizing predictive maintenance in the mining industry?
IIoT technology allows mining companies to monitor equipment in real-time, detect potential issues before they occur, and optimize maintenance schedules.
What are the key components of an effective predictive maintenance strategy?
Key components include data collection and analysis, condition monitoring, predictive analytics, maintenance planning, and continuous improvement.
How does data analytics play a role in predictive maintenance for mining equipment?
Data analytics helps mining companies analyze large volumes of data to identify patterns, trends, and anomalies that can predict equipment failures.
What are some common predictive maintenance techniques used in the mining sector?
Common techniques include vibration analysis, oil analysis, thermography, ultrasonic testing, and equipment performance monitoring.
How can predictive maintenance help ensure safety and compliance in the mining industry?
Predictive maintenance helps mining companies identify and address safety hazards, comply with regulations, and prevent accidents and injuries.
How can predictive maintenance help maximize efficiency and productivity in mining operations?
By reducing downtime, minimizing disruptions, and optimizing equipment performance, predictive maintenance can improve overall efficiency and productivity.
What are some future trends in IIoT and predictive maintenance for mining equipment?
Future trends include the use of artificial intelligence, machine learning, and advanced sensors to further enhance predictive maintenance capabilities.
How important is training and skill development for implementing predictive maintenance programs in the mining industry?
Training and skill development are crucial for successfully implementing predictive maintenance programs, as they ensure that employees have the knowledge and expertise to effectively use new technologies and techniques.
How can companies measure the ROI of their predictive maintenance initiatives in the mining industry?
Companies can measure ROI by tracking key performance indicators such as equipment uptime, maintenance costs, energy consumption, and production output before and after implementing predictive maintenance initiatives.